Hierarchical Lattices in the Automotive Industry
Our guest contributor for this blog post is Dr. Herderick, a materials science expert and thought leader in additive manufacturing.
As far as safety is concerned, it is hard to compete with lattices’ promising potential as effective and efficient materials configurations for reducing injury and trauma.
In our last blog post, we introduced the concept of lattice structures as they pertain to military helmets. Their potential applications in helmet safety are many, but what makes lattices so powerful is their ability to become what is known as hierarchical lattice structures. In other words, lattice structures are built upon lattice structures.
Lattices are attractive configurations because they handle impact energy very well compared to denser, less complex structures. The geometry of the lattice is what makes them perform so effectively in a variety of applications and scenarios.
For example, when helmets use only one gradient type of padding, they tend to modulate energy less efficiently as compared to structures that rely on more complex gradients. Additive substances like lattices fill this gap, offering a customizable, flexible, and above all, stronger solution than typical materials.
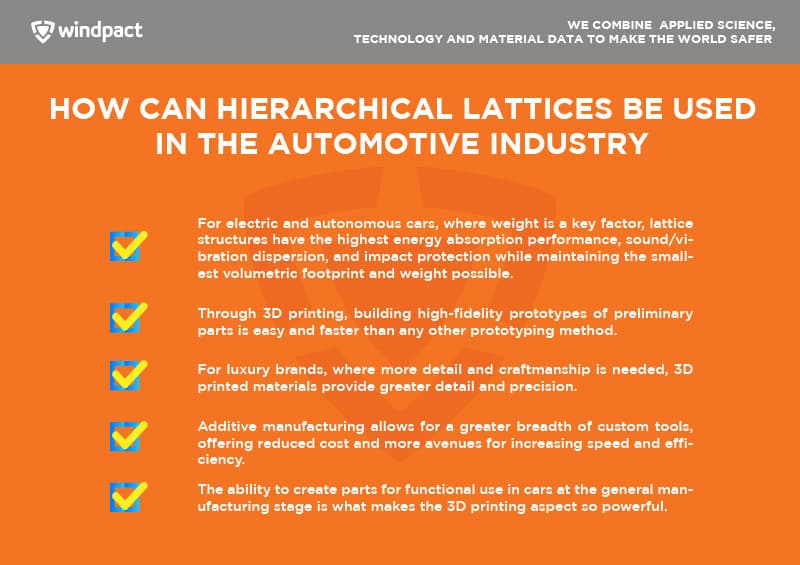
While hierarchical lattice structures are being explored for their potential usefulness in military safety gear, the automotive industry has only begun to notice their full potential. According to the National Highway Traffic Safety Safety Administration’s (NHTSA) most recent annual report, the field faces a massive challenge of designing safer vehicles that reduce the number of injuries from car crashes, made even more complicated changing behavior of a growing population.
In our next dive into lattice applications, we will be dissecting:
- How far lattice structures have come since their initial appearance in design space.
- How 3D printing optimizes materials for automotive safety.
- The way hierarchical lattice structures are being used in the automotive industry as a whole.
Why are lattices an attractive choice for engineers?
Lattices offer transformational potential for controlling and tailoring properties in many applications in ways that traditional materials cannot.
When a material is converted into a cellular solid, the specific properties of a material such as strength/density or impact absorption/weight can be engineered. Additive manufacturing (AM) enables revolutionary materials like lattices to be made that couldn’t have been made any other way.
Think about it this way: we are surrounded by cellular structures, meaning structures that are made out of smaller components, and demonstrate properties of tension and strength that are more dependent on their topology than on their material composition type.
For example, look at truss bridges. Their high load-bearing capacity is made possible by the series of trusses that distribute stress across the struts. These lattice materials have received much more attention from engineers and designers for their lighter weight potential compared to traditional material choices.
Through the advent of AM, it is now possible to create materials while manipulating their structure across length scales from microns to meters.
This ability to design structure and microstructure across length scales is why lattice-based materials can exceed the performance of traditional materials.
AM makes it possible to manipulate macroscopic scale theoretical principles like truss theory in the case of truss bridges into microscopic materials composites such as in lattices. This paves the way for greater flexibility in terms of application specific properties can be chosen for a given application.
In being able to manipulate materials design on length scales that determine macroscopic properties, engineers can create devices, parts, and components that are created exactly for their intended purpose. In this sense, lattices are the answer to years of these practical design roadblocks.
What are the applications of additive manufacturing in automotive safety?
Additive manufacturing itself is quickly becoming a pivotal part of the automotive industry’s design process, namely by introducing superior speed, customization, tools, and general parts manufacture. Specifically, additive manufacturing has made huge strides in:
Prototyping
Rapid prototyping has almost become synonymous with AM principles, as the speed at which preliminary parts can be manufactured into high-fidelity prototypes is only made possible with the advent of additive manufacturing.
While low-fidelity prototypes are effective in many situations, it is hard to beat the noticeable gains in preliminary design when using AM technology for rapid prototyping.
High-performance parts with deeper complexity
This is especially true for luxury and classic models, where fine detail and craftsmanship make or break a model. With AM materials, greater specificity in design and applications makes for more vivid detail and precision, evident in brands like Bentley and Volkswagen.
Producing manufacturing tools
Automotive manufacturers use hundreds if not thousands of custom rigs, parts, and fixtures each with varying degrees of specificity and applications. Additive manufacturing allows for a greater breadth of custom tools, offering reduced cost and more avenues for increasing speed and efficiency.
High performance parts and systems fully printed
This is probably the newest, most exciting part of AM that has many manufacturers trying to hop on the bandwagon as soon as possible. The ability to create parts for functional use in cars at the general manufacturing stage is what makes the 3D printing aspect so powerful.
With additive manufacturing, it is now possible to meet design and mechanical specifications with precision specificity, as well as improve metrics in base parts themselves, such as their weight. For example, Volkswagen redesigned a reinforced A-pillar window support, which now weighs 74% less than its original.
As AM starts to become comparable in cost to traditional methods like molding and die-casting, more manufacturers may be inclined to embrace additive manufacturing.
While these AM technologies are attractive for many reasons, very few manufacturers use them for parts that need to meet stringent safety standards.
While additive manufacturing makes for compelling replacements to traditionally-casted parts and materials, their ability to stand against the many safety scenarios necessary to protect motorists properly is still being investigated.
How can hierarchical lattices be used in the automotive industry?
Macro trends in automotive design are moving in a substantially different direction than it did even a decade ago. Electrification and autonomous vehicles (aka, self-driving cars) are increasing in popularity, with sales of electric cars surpassing 2019’s sale of 2.1 million vehicles, to exceed the stock to 7.2 million electric cars for 2020.
However, with electrification and autonomy comes one key caveat: weight. Increased weight in both aerospace and automotive industries has remained an issue, but the added weight of batteries and electronics combined with the mission for creating vehicles with the longest distance range possible makes for a quite a heavy vehicle regardless of other factors.
Coupled with more competition for limited space within the car’s frame, you have a hefty vehicle that is weighed down by everything it needs to function properly.
This, of course, is where hierarchical lattices produced by additive manufacturing come to the rescue. Lattice structures have the highest energy absorption performance, sound/vibration dispersion, and impact protection while maintaining the smallest volumetric footprint and weight possible.
As electrification and self-driving cars gain greater traction, there is going to be a very real need for lightweight replacements that offer comparable physical properties to traditional parts.
Windpact recognizes this need, and has been actively generating solutions that strike the proper balance between safety and functionality. We maintain a robust, efficient pipeline for maximizing client’s specifications, whether it be a goal of reducing weight, bulk, or cost.
We apply a predictive computational model that is workable for hierarchical lattice structures. From here, we test various configurations of the structure against different outcomes. Then, we optimize the configuration’s impact attenuation potential, applying real-world scenarios to ensure the part being designed functions precisely as it should.
As more materials become available for additive manufacturing, Windpact is ready to incorporate, execute, and improve upon the methods that make lattice structures so effective in impact science.
Closing Thoughts
Creating competitive lattice structures for a changing automotive world means, first and foremost, remaining on top of the latest trends guiding additive manufacturing. Our team at Windpact understands the demands of automotive engineers and designers in meeting the challenges of safety, ingenuity, and innovation.
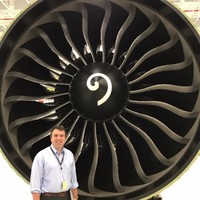
Ed Herderick is the Director of Additive Manufacturing at The Ohio State University Center for Design and Manufacturing Excellence (CDME). He is responsible for all additive activities supporting CDME’s mission to provide industrial education to students, user facilities for faculty and partners, and bringing manufacturing innovation to the industry.