How Finite Element Analysis Makes Ballistic Helmets Better
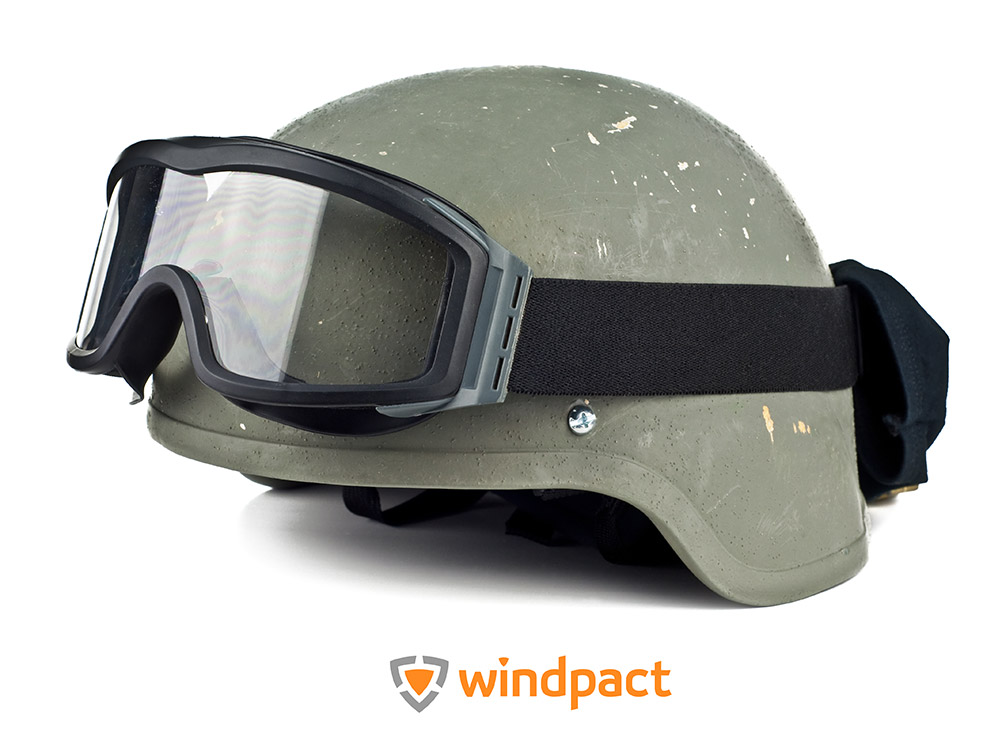
Simulating the effect of a bullet’s impact on a helmeted human head is challenging to do, especially because the mechanics underlying head injury as a result of ballistic impact are not well-defined.
Finite Element Analysis (FEA) is proving to be an increasingly effective tool for accurate simulations of a helmet’s behavior and even in assessing how well a helmet protects the user from a skull fracture. However, there remains a gap in the literature that adequately addresses ballistic impact testing on helmets.
Recent research from the Center for the Technology of Health in Sweden (CTHS) aims to close the gap. Their research used FEA methods to not only generate a predictive workup of helmets sustaining ballistic projectile impacts, but also the effect of localized helmet structural failure on the human skull.
Modeling Ballistic Helmet Impacts Using FEA Methods
Finite element analysis (FEA) can allow designers to see how a helmet behaves under various loading conditions before generating a physical sample. This is an invaluable capability in product development because it minimizes the time and expense of building effective solutions.
For example, even though many ballistic helmets stop bullets from full penetration, the wearer is still at high risk for injury. The team from CTHS used FEA to analyze a class of these injury types, commonly known as “rear effect.” The rear effect refers to when the inward deformation of the inside of the helmet shell strikes the skull, despite stopping the projectile from fully penetrating the helmet.
Given the multitude of potential variables that can affect ballistic helmet performance, such as bullet caliber, impact angle, etc., it can be nearly impossible to test for all impact conditions.
As a result, most researchers attempt to simplify the challenge by focusing on head-on or direct impacts, despite the fact that oblique impacts are thought to have a greater potential for causing brain trauma.
The team at CTHS sought to investigate two issues that have been largely ignored by others:
- Incorporate a validated head and brain FE model into a ballistic helmet model with the purpose of identifying how the helmet stiffness affects the head and brain trauma.
- Utilize the FE model to investigate various bullet impact angles and accompanying head and brain trauma.
This FEA research revealed a few key insights:
- As the angle of impact increased, more kinetic energy from the bullet was transferred to the helmet
- Lower helmet stiffness leads to more severe helmet failure
- Higher helmet stiffness results in an increase in cranial pressure
- Bullets that struck at a 45-degree angle caused the most strain in the brain
The study team acknowledged that while the FE modeling was successful in predicting skull trauma, that it is difficult to have a similar level of confidence in predicting brain trauma because there is not a clear link between strain in the brain or intracranial pressure and brain trauma.
In other words, it is possible to predict if a user will suffer a skull injury after a bullet impact when using a helmet but it is unclear is how these same impacts directly affect the brain and clinical outcomes.
How Ballistic Impact and Blunt Helmet Impact Fundamentals Are Related
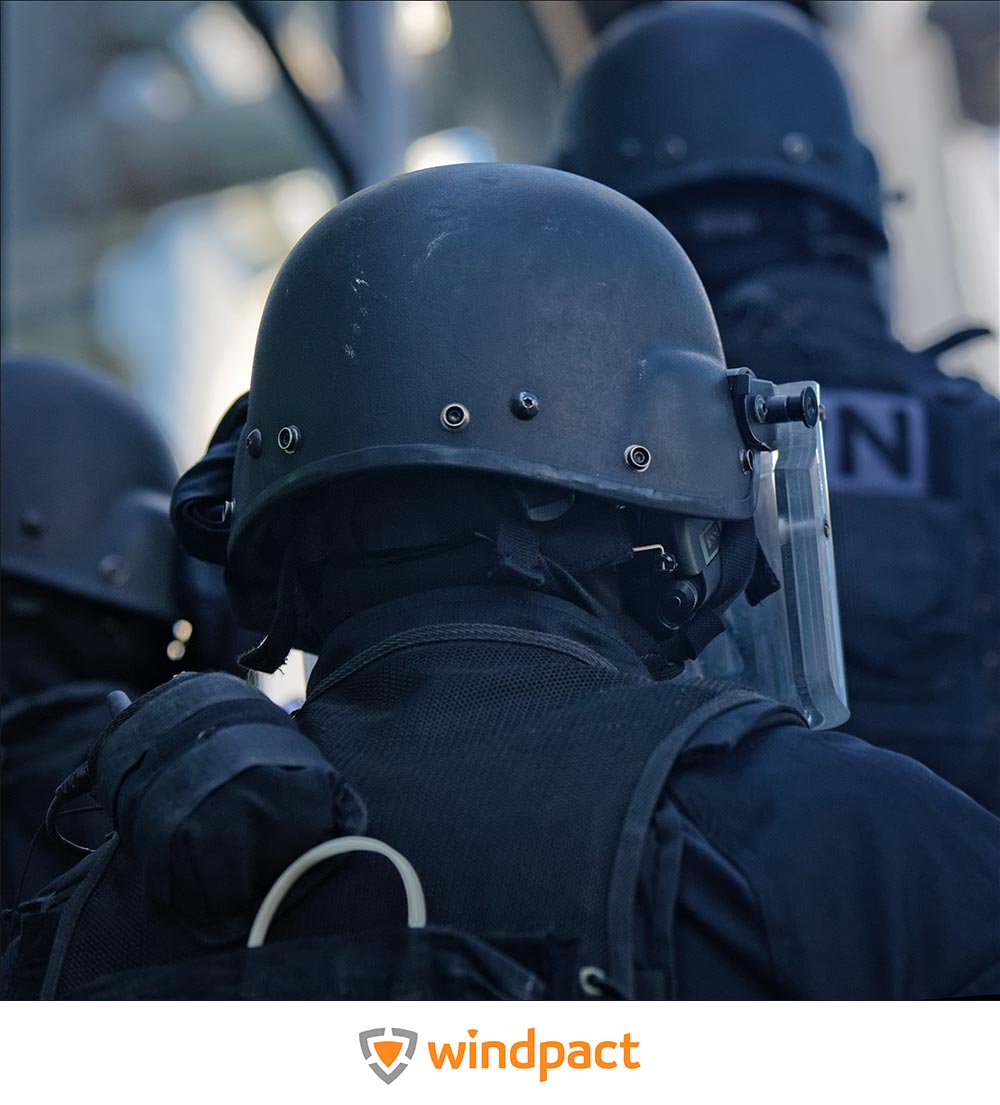
In some regards, a bullet striking a helmet and a baseball hitting a helmet are very different types of impact—one is a high-speed, low mass event, and the other is a low-speed high mass event.
But the factors that are necessary considerations when modeling either impact are similar – material characterization, helmet structure, padding configuration, etc., and Windpact has the developed the unique expertise to analyze all of the factors that underlie the accuracy of FEA simulation.
How Windpact’s FEA Modeling Delivers Market Benefits
Windpact utilizes proprietary FEA techniques to efficiently and effectively develop superior products and technologies. This type of modeling allows for a more effectual model that mirrors real-world behavior and accomplishes several things throughout the chain of development of a product.
Namely, FEA modeling offers sustainable gains, including:
- Cost: by using machine learning methods that predict model behavior before hard prototypes are created, costs related to continued prototype testing are minimized.
- Time: the use of a dynamic, input-driven system not only reduces cost but also reduces the time needed to create multiple models through rote methods.
- Design: customizable and versatile models generated through FEA methods encourage designers to take risks and create a better product that ultimately saves both time and money.
In combination with a proprietary database of validated foam materials, each model generated through our FEA approach is optimized, driving solutions through superior performance and protection. The same approach towards modeling ballistic impact behavior also drives innovation in motor vehicle safety, helmet safety, and informing regulatory guidelines.